What is Thermoforming?
Thermoforming is a plastic manufacturing process that Elmes Packaging uses to create plastic packaging products. Thermoformed packaging has many advantages over other types of packaging manufacturing, including increased durability, recyclability, potential for customizability and lower tooling cost.
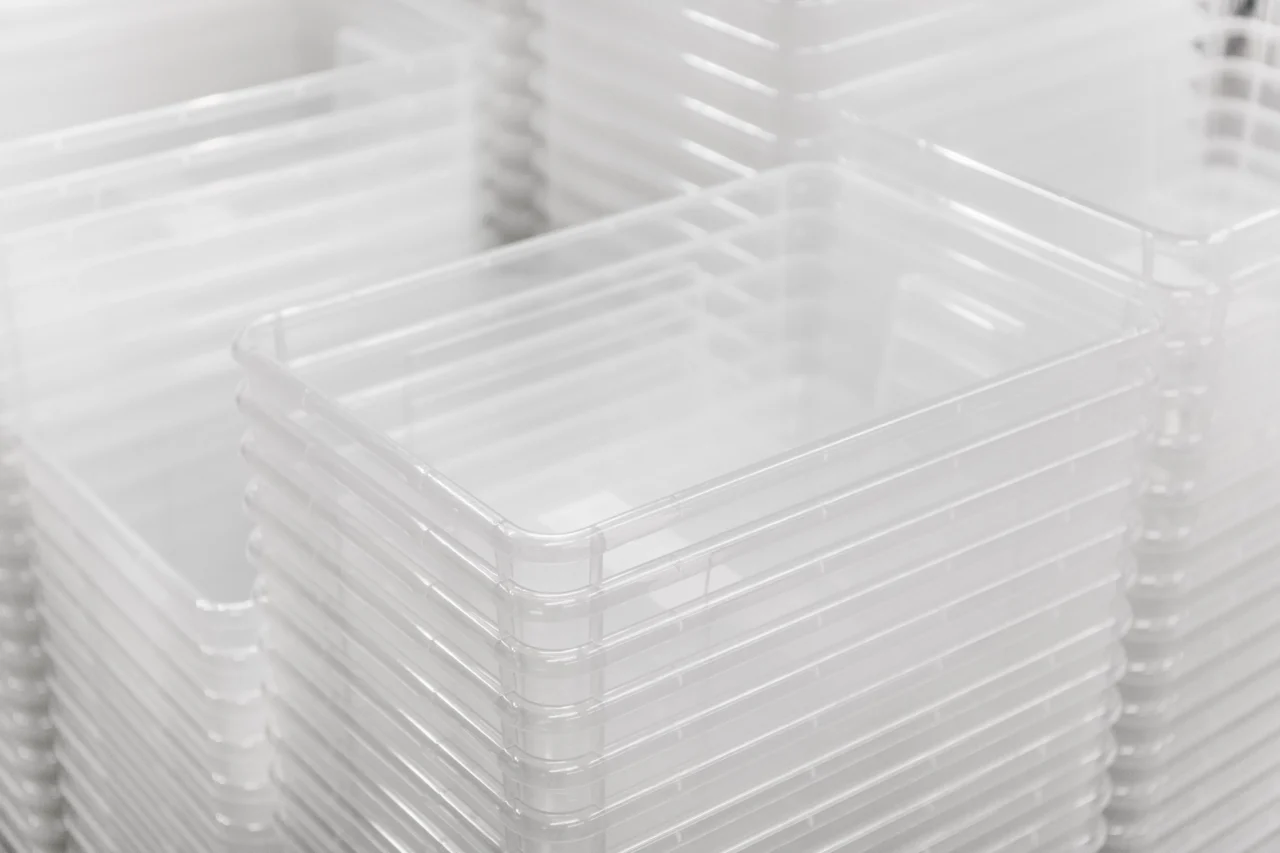
How Does Thermoforming Work?
The thermoforming process begins with a flat sheet of thermoplastic material. Thermoplastic materials are substances which are solid at room temperatures but are able to be reshaped when heated. The name “thermoforming” comes from the process of heating a plastic sheet until it becomes pliable, and then shaping it into a specific form using a mold. When the plastic cools, it retains the shape of the mold, resulting in a durable and lightweight product. The formed plastic is then trimmed to create the final product.
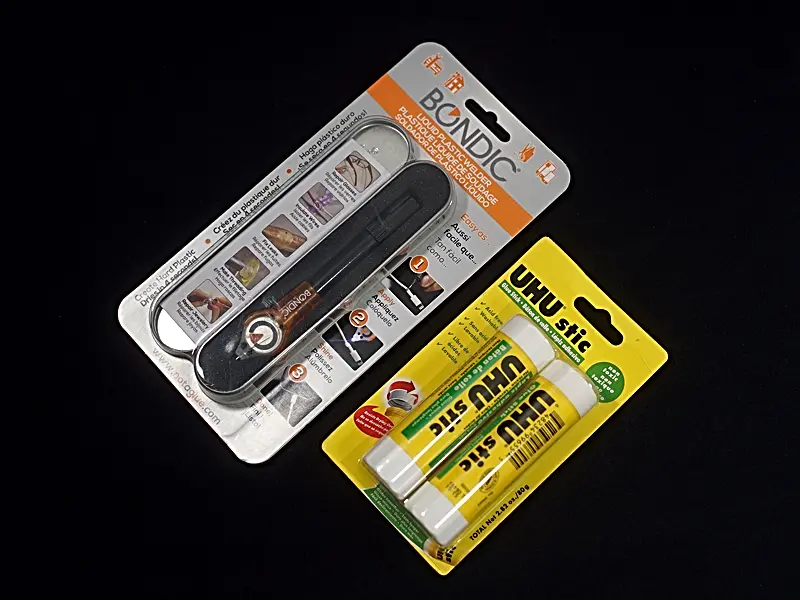
Applications of Thermoformed Packaging
Thermoformed packaging is widely used across a variety of industries due to its durability, low shipping cost, recyclability and cost-effectiveness. Common applications include:
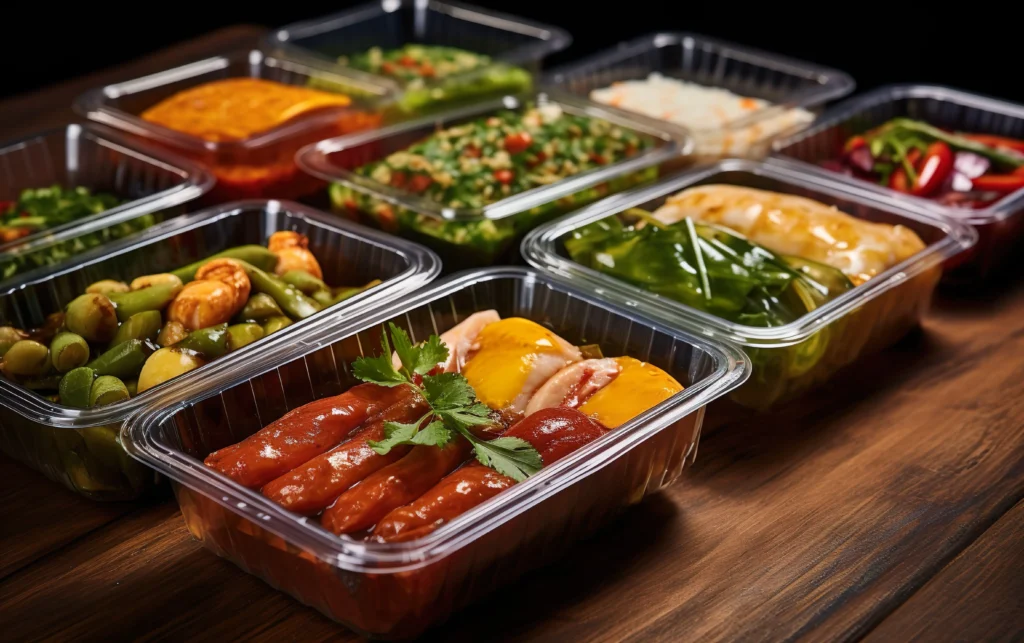
Thermoformed trays, containers, and lids are widely used in meat, produce, and other food packaging because of their ability to keep food products fresh and protected.
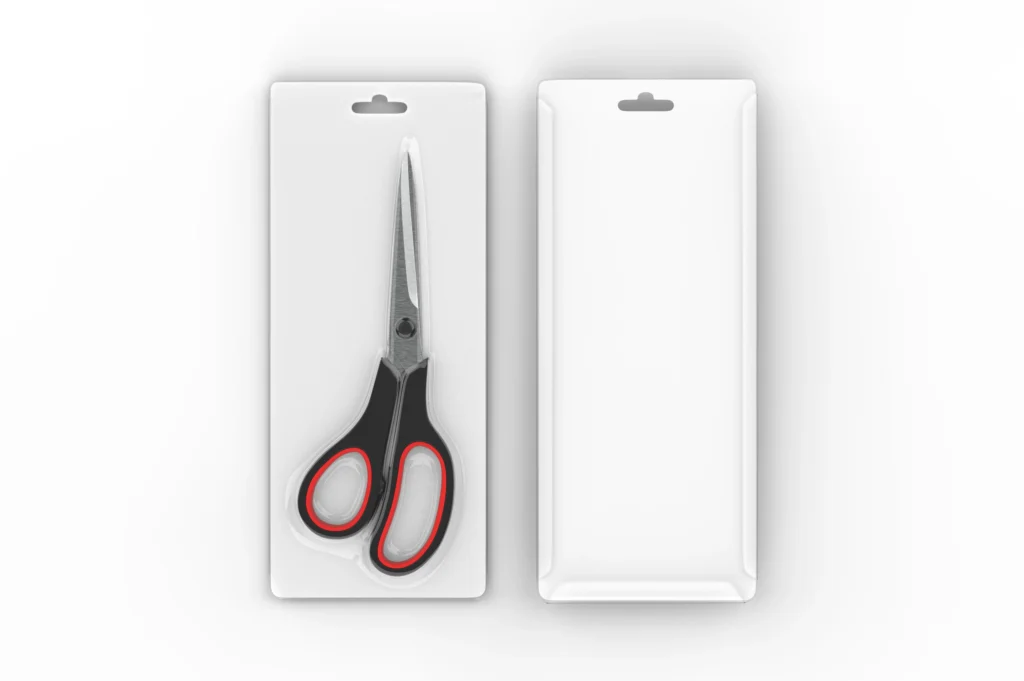
Many everyday items are packaged in thermoformed packaging such as blister packaging and clamshells because of their durability, presentability and customizability.
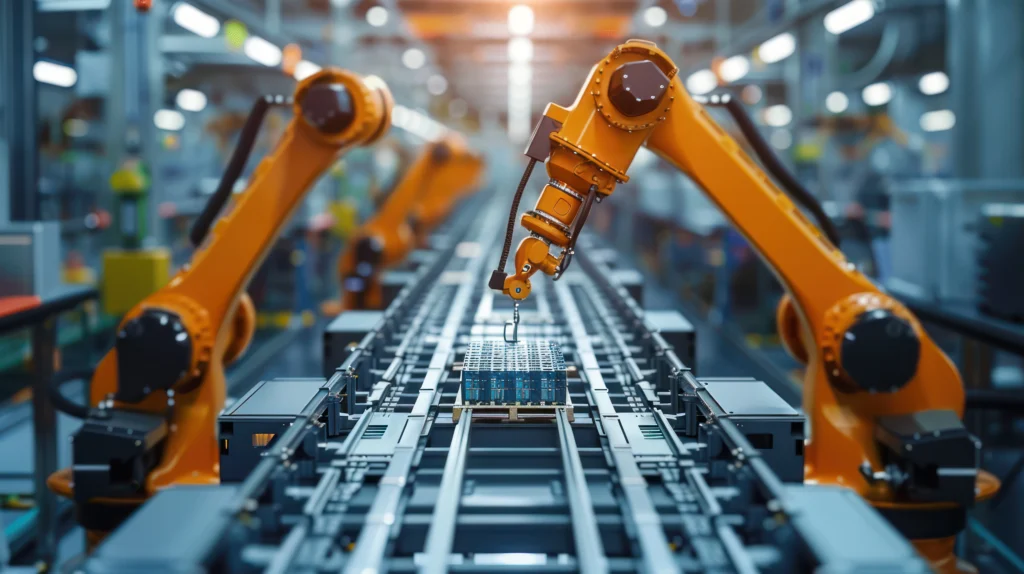
Thermoformed trays are an ideal solution for a wide variety of manufacturing applications, serving as storage and shipping platforms.
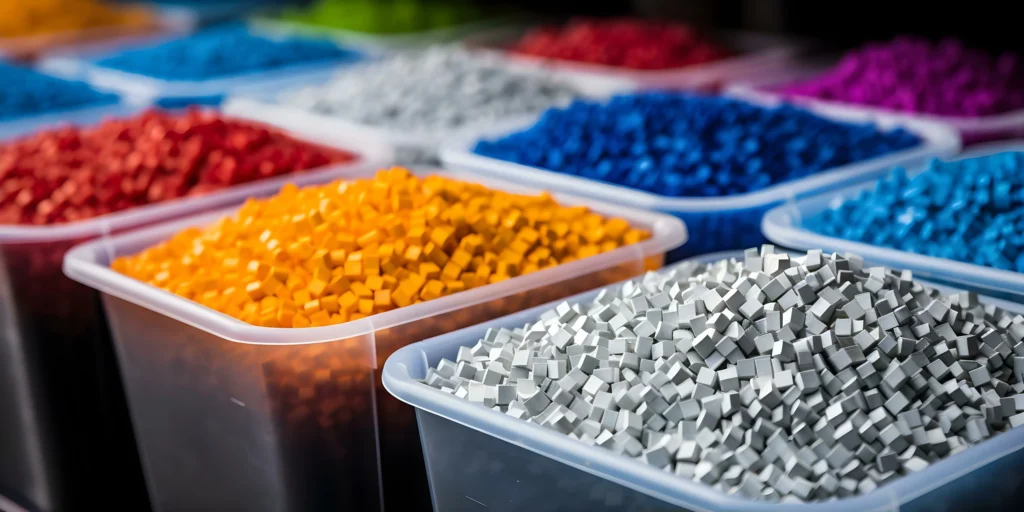
Benefits of Thermoformed Packaging
- Cost-Effective Production: Thermoforming is an economical option for packaging production. Compared to other types of packaging manufacturing, thermoforming is an efficient process, enabling high-volume production while maintaining quality. Thermoforming materials are also less expensive than some other common packaging materials like glass or paper.
- Customization and Flexibility: Thermoforming offers a high degree of design flexibility. Elmes Packaging specializes in creating custom molds to produce packaging that fits the specific dimensions and requirements of our customers’ products. This flexibility also means packaging can be easily customized for branding purposes.
- Lightweight and Durable: Thermoformed packaging is highly robust, meaning it can protect products from damage during shipping and storage. It’s also very lightweight, which reduces shipping costs and makes it easier for consumers to handle.
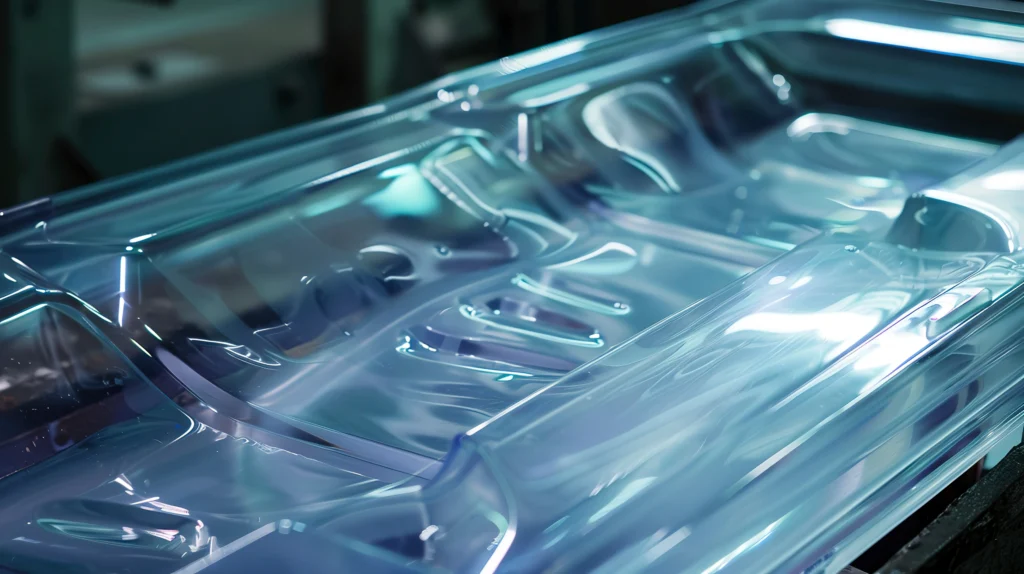
Thermoforming and Sustainability
Sustainability in the packaging industry is a complex issue. While improperly discarded plastic waste is a growing environmental issue, there will always be a need to safely package goods. Thermoforming decreases the environmental costs in terms of emissions involved in their manufacture and transportation compared to other manufacturing processes.
Elmes Packaging is committed to pursuing sustainable manufacturing, including the use of recycled and recyclable materials and minimizing plastic waste.
Contact Elmes Packaging to Learn More
Here at Elmes Packaging, we pride ourselves on providing practical thermoformed packaging solutions that meet a wide range of industry needs — from Food, to consumer goods to manufacturing packaging needs and more.
For more information about Elmes Packaging’s approach to thermoforming, you can learn more about Our Process or contact us to discuss how we can assist you by providing safe, reliable, and customized thermoforming packaging solutions.